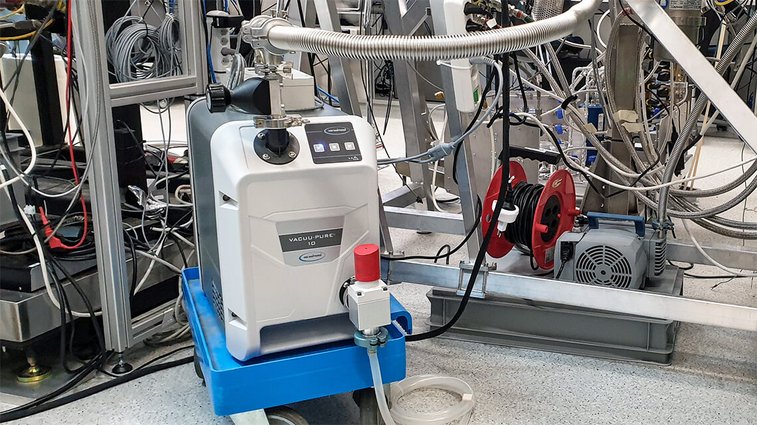
VACUU·PURE® screw pump on a magnetron sputtering system
© ETH Zürich
Clemens Todt conducts exciting basic research at the Swiss Federal Institute of Technology in Zurich (ETH), where he is a doctoral student in the Laboratory of Solid State Physics. The results of his Advanced Semiconductor Quantum Materials group, led by Professor Wegscheider, could optimize the properties of quantum computers in the future. In the interview, Clemens Todt tells how the VACUU·PURE® 10 screw pump supports their work.
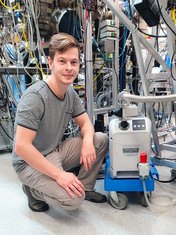
Clemens Todt is a doctoral student at the ETH Zurich.
© ETH Zürich
What is your research group's topic?
Clemens Todt: We are engaged in crystal growth. Our expertise lies in the fabrication of III/V semiconductor heterostructures, of which 2-dimensional electron gases are our specialty. This requires an enormous effort. This is why groups working at the same level in our niche are rare. Our work is at the beginning of the value chain and the highly complex samples go to research groups all over the world.
My focus is the interaction of semiconductors with superconductors. Here we are trying to collaborate on a new area of research. The topic has only become really interesting since 2012, and there is a lack of fundamentals on how to combine the two material systems. It's still up in the air, but the results could be important for quantum computers. We are researching a way to reduce their susceptibility to interference.
What different methods do you use?
Clemens Todt: For semiconductor heterostructures, we use the molecular beam epitaxy (MBE) growth method – a physical gas deposition process. The significant advantage here is that we can grow complicated layer sequences of different materials with atomic precision. Among other things, this method is suitable for low-melting metals such as indium or gallium. They are vaporized and form a directed molecular stream under vacuum onto the surface of a carrier layer – called substrate or wafer. Atom by atom, they settle on the wafer in a desired structure and crystallize into thin films.
Our superconducting layers, on the other hand, are based on niobium. This metal has an enormously high melting point of 2,500°C. In the process, the entire system heats up and foreign atoms diffuse out of the steel. As a consequence, the sample can be damaged in the process. Subsequently, we decided to use an alternative deposition process: magnetron sputtering. In this process, the metal is placed in a chamber into which we feed argon. At pressures of 1 x 10-3 mbar to 5 x 10-2 mbar, we ignite an argon plasma. The argon ions strike the surface of a coating material, a so-called target made of niobium, and tear out material. These knocked-out particles then migrate to the wafer and deposit there as layers.
What do you need vacuum pumps for?
Clemens Todt: As part of my doctorate, I built a new magnetron sputtering system. It's challenging, but I enjoy the tinkering; we even had to final-assemble the cryopumps. They suck in the argon at 1,500 liters per second. The cryopump has cold surfaces inside that "trap" the individual atoms. Once the cryopump fills up, we have to regenerate it. Now another vacuum pump comes into play – the fore pump. To regenerate the cryopump, we heat it up. In the process, the gases are released and pumped out by means of the fore pump. When the cryopump is pumped empty, the pump and chamber must be brought to the necessary vacuum under which the cryopump can cool down again.
Cryopumps
Cryogenic vacuum pumps belong to the adsorption pumps and are therefore gas-binding pumps. Inside the pump, surfaces are cooled down to a few Kelvin. Molecules and atoms can condense on these as in a kind of freezer. The regeneration of the cryopump proceeds as follows: The valve is closed and the pump is warmed up to ambient temperature. This causes the molecules to desorb, i.e. to return to the gas phase. These gases can now be pumped out by a fore pump. The vacuum of the fore pump then serves as thermal insulation, under which the cryopump can cool down again.
Due to their design and large flange diameters, extremely large pumping speeds are achievable with cryogenic pumps. The use of cryogenic pumps is a way to evacuate large-volume vacuum chambers to ultra-high vacuum in a realistic time frame under clean conditions.
Why is cryopump regeneration so important?
Clemens Todt: Our high purity plants are absolutely "sacred". Our defects in the crystal lattice are 1013 per 1024 atoms per cubic centimeter. So we have eleven orders of magnitude before we find an atom, which we don't want. When the cryopump is regenerated, contaminants from the fore vacuum pump can enter the system, such as moisture from the air, oil, abrasion. When the chamber is back in a high vacuum state, we can detect the contaminants with a mass spectrometer. We want to avoid these contaminations with absolutely clean fore pumps.
In the past, we tested various technologies for this: For example, we tried using a turbopump and a diaphragm pump as a fore pump. However, the turbo pump is oversized for this purpose and the bearings break down over time due to vibrations. In addition, I tried out different scroll and screw pumps. The pumps tested up to that point either produced abrasion or heated up because of the outgassing argon and eventually seized up.
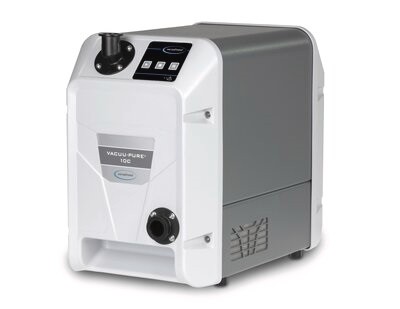
High-purity screw pump VACUU·PURE®
How was VACUU·PURE able to succeed?
Clemens Todt: Before using it on our sensitive plant, we precisely investigated whether the VACUU·PURE screw pump could be used in our plant. For the regeneration of our cryogenic pumps, we were looking for a robust and high-purity vacuum pump: this must have a base pressure of at least 10-2 mbar. In addition, a sufficiently high pumping speed is required to cope with the escaping gases from the cryopump. Of course, it is also essential that it is absolutely oil-free and particle-free.
VACUU·PURE met all these requirements. We tested the pump on a cryogenic pump on a test chamber. The screw pump handled the amount of argon gas without seizing. In addition, we could see in the mass spectrometer that it did not bring oil or other hydrocarbons or abrasion into the system. Therefore, we subsequently added the new vacuum pump to the actual "sharp" magnetron sputtering system.
Are there any other special features of VACUU·PURE?
Clemens Todt: The beauty of VACUU·PURE is that it is a small compact cube. We can easily move the vacuum pump from A to B for our various applications. Then just plug it in, turn it on, and we're done. We also attached a small pressure sensor. This communicates with our database via Wifi. No matter where the pump is: We always automatically see the current prevailing pressure.
Do you use VACUU·PURE for other tasks?
Clemens Todt: I use it to purge the high-purity gas supply system of the magnetron sputtering system. To do this, we pump down the line to the screw pump's base pressure of 10-3 mbar, fill to just above atmospheric pressure with argon, and pump down again. We do the whole thing a couple of times. After that, we completely heat up the lines for maximum purity. Here, too, the resistance of VACUU·PURE to argon has been demonstrated.
In addition, VACUU·PURE is also used on the UHV systems to generate the rough vacuum.
Advantages of VACUU·PURE® 10C
• Ultimate vacuum of 10-3 mbar
• Pumping speed of 10 m3/h
• 100% oil-free, without hydrocarbons
• Abrasion-free, without particles
• Ideal for regeneration of cryopumps
• Suitable for pumping light gases such as argon
• Compact design
How is the cooperation with VACUUBRAND?
Clemens Todt: I like to tell people that my main job is active problem solving. (Laughs) A good example is finding the right vacuum pump to regenerate the cryogenic pumps. Fortunately, I never had any problems with VACUUBRAND – the pumps just run. The products have proven themselves for us. For example, we already use many of their diaphragm pumps. With the VACUU·PURE screw pump, we have now added a great new product to our equipment.
We thank Mr. Clemens Todt and ETH Zurich for the interview.