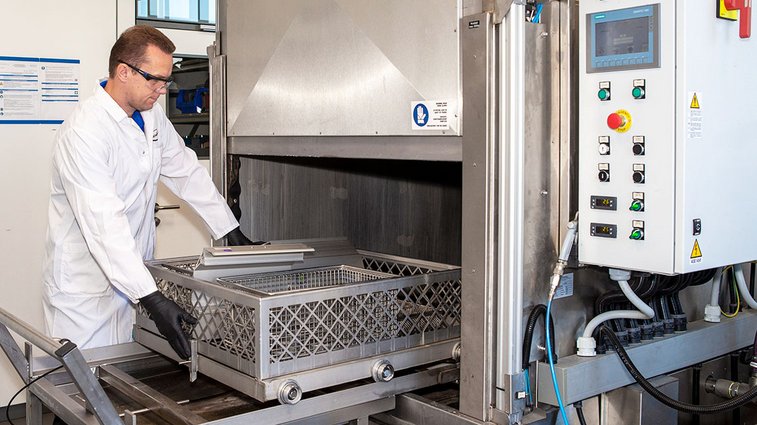
Service technician Max Werner at the decontamination cell of VACUUBRAND for used vacuum equipment
Vacuum equipment comes into contact with numerous substances in the laboratory. In addition to harmless substances, these can also be aggressive, harmful chemicals or infectious biological material, for example. If the equipment is then serviced or repaired at VACUUBRAND, strict protective measures are necessary for the welfare of our service team. Since occupational safety is our top priority, we operate an in-house decontamination cell as part of our quality management. This allows us to decontaminate used vacuum equipment from many hazardous substances.
What is the purpose of decontaminating the vacuum devices?
Our vacuum pumps come into contact with many different substances – including substances that are harmful to health. We naturally want to offer maintenance or repair to as many customers as possible. However, at the same time, we need to protect the health of our employees. That is why all products sent in are first cleaned in our company's own decontamination cell. As soon as they are decontaminated, our service team can check, maintain or repair them without any risk.
Why does VACUUBRAND operate its own decontamination cell?
Initially, we carried out the decontamination of vacuum pumps externally. However, over time, we took a closer look at the issue of occupational safety and that's why we decided to set up our own decontamination cell. Thanks to this, we were able to decontaminate all vacuum equipment in-house from then on. The facility even exceeds the specifications of the Federal Institute for Occupational Safety and Health (baua) for handling hazardous substances. To ensure process safety, the work procedures are embedded within our quality management. Today, the decontamination cell enables us to totally clean our equipment from many substances and thus ensure the safety of our specialised service staff. Our highly qualified team is extensively trained and receives quarterly training updates on the decontamination procedures.
Which substances can VACUUBRAND decontaminate?
Internal safety officers, chemists and our occupational safety specialist decide which substances we can decontaminate from our equipment:
- In our decontamination cell, we can decontaminate equipment arising from many chemicals (e.g. organic solvents) and biological material up to risk group 1 (e.g. lactobacilli or baker's yeast).
- A special case is equipment that has been in contact with biological substances of risk group 2 (e.g. measles virus). These must be completely disassembled and decontaminated by the user before shipping.
- In contrast, devices with contact to biological substances of risk group 3 (e.g. yellow fever virus) or 4 (e.g. Ebola virus) are generally excluded from maintenance and repair.
How does a service case proceed at VACUUBRAND?
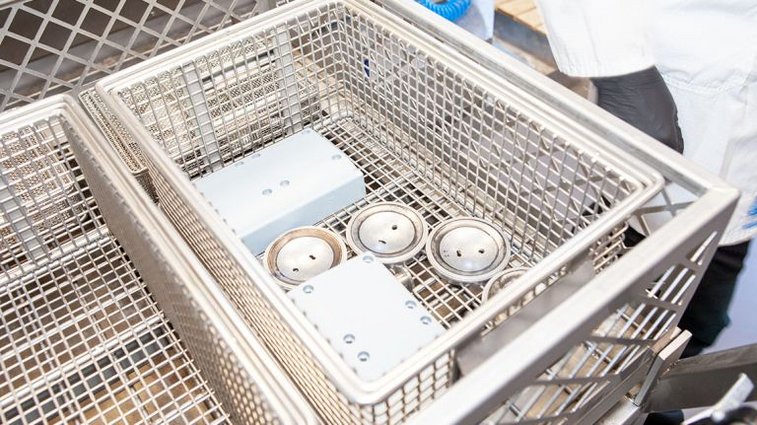
Equipment parts for decontamination in the cleaning plant
Decontamination follows a precisely defined procedure:
- Protective measures: The decontamination cell is a closed unit in which there is constant air circulation. In an entrance airlock, our staff puts on appropriate protective equipment: always work safety shoes, protective gloves, safety goggles, work coats as well as protective clothing (e.g. long trousers) – in case of high risk, respiratory masks with special filters and gloves are also worn.
- Incoming inspection and dismantling: Upon receipt, our employees carry out a technical and electrical safety inspection, check for radioactivity, measure performance data and dismantle the unit.
- Decontamination: All equipment parts are put through an ultrasound-assisted cleaning system. Here they are effectively and gently decontaminated.
- Maintenance or repair: Then the actual maintenance or repair process can take place. Finally, the repaired device undergoes a complete testing procedure as with new products. Therefore, the customer receives their equipment reconditioned and as good as new.
How can customers prepare their vacuum devices for maintenance or repair?
With all vacuum devices, the first question to ask is: What substances have they come into contact with? This is why it is absolutely essential that customers inform our service team at VACUUBRAND before shipping by filling out a clearance certificate. Only this enables us to make a realistic risk assessment of the desired maintenance or repair. Our trained personnel can then take the appropriate protective measures in the decontamination cell. A detailed explanation of the procedure (filling out the clearance certificate, packing and shipping the product) can be found on our website.
If you have any questions, please do not hesitate to contact our service team: