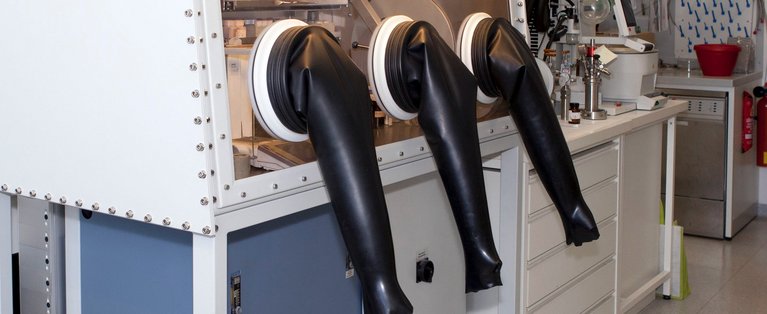
Glovebox
Vacuum is required at the glovebox for three different processes: Pressure stabilization in the glovebox, the inertization process of the airlocks and the regeneration of the various filters.
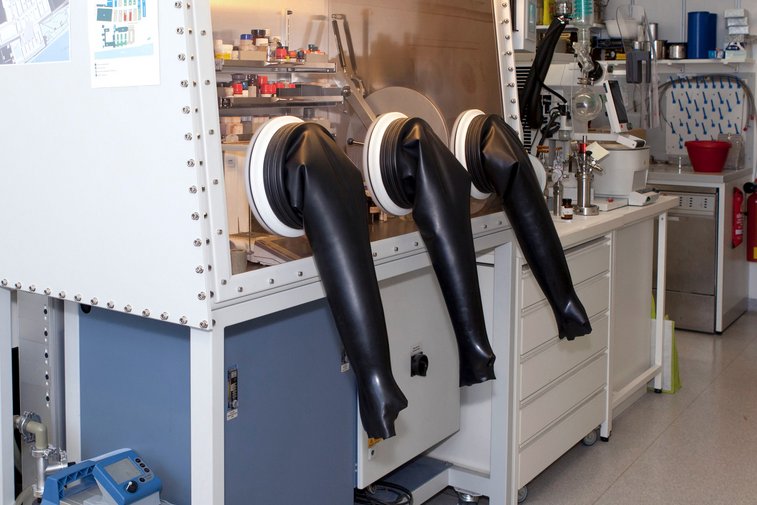
Vacuum for gloveboxes
Replace or supplement rotary vane pumps with chemistry diaphragm pumps
The most common tasks for the vacuum pump on the glovebox are the inerting process of the airlock and equalizing the working pressure inside the chamber. Pressure equalization does not make any extraordinary requirements on the vacuum pump. During inertization, the airlock is first evacuated in several cycles and then flooded with inert gas. In order to achieve a sufficiently low residual oxygen content, a vacuum pump with an ultimate vacuum in the range of 10-3 mbar is required in many cases. Depending on the size of the airlock, a correspondingly high pumping speed is required to evacuate the airlock quickly.
Two-stage rotary vane pumps fulfill these requirements very well. However, they require oil as an operating medium and are prone to corrosion. It should therefore always be checked whether the requirements can also be met with a suitable chemistry diaphragm pump and additional pump-down cycles.
The combination of a rotary vane pump with a chemistry diaphragm pump as a backing pump offers the advantage that the maintenance intervals of the rotary vane pump are significantly extended and oil changes are significantly reduced, especially for frequent airlock operations. In this arrangement - controlled via a corresponding valve control with a DCP 3000 - the airlock is first pre-evacuated by the diaphragm pump before the rotary vane pump is switched on.
Important questions on vacuum technology
The most common tasks for the vacuum pump on the glovebox are the inerting process of the airlock and the equalization of the working pressure inside the chamber. Our vacuum pumps are suitable for gloveboxes with relative positive and negative pressure. Pressure equalization does not present any extraordinary requirements for the vacuum pump. When evacuating the airlock, the requirements for the vacuum technology vary depending on the size of the airlock, the required residual oxygen content or the number of gloveboxes.
Depending on the desired residual oxygen content, the maximum ultimate vacuum of diaphragm pumps is not always sufficient for inerting the airlock. In addition, more inerting cycles are required. In many cases, rotary vane pumps are therefore used for this task. They are powerful in the range of 10-3 mbar and can quickly reduce the residual oxygen content in the airlock to the desired level. The disadvantage compared to diaphragm pumps is the need to use oil as an operating medium and the lower corrosion resistance. Maintenance costs are therefore significantly higher.
It is therefore always advisable to check whether the rotary vane pump can be replaced or supplemented by a chemistry diaphragm pump. Chemistry diaphragm pumps are oil-free, chemically resistant and durable. VARIO diaphragm pumps with VARIO technology regulate the vacuum according to the need via the motor speed. Compared to a rotary vane pump, they are therefore significantly more efficient and quieter. They also require hardly any maintenance.
The two pump technologies can also be used together. The combination of a rotary vane pump with a chemistry diaphragm pump as a backing pump offers the advantage that the maintenance intervals of the rotary vane pump are significantly extended and oil changes are significantly reduced, especially in the case of frequent airlock processes. In this arrangement - controlled via a corresponding valve control with a DCP 3000 - the airlock is first pre-evacuated by the diaphragm pump before the rotary vane pump is switched on.
The savings in operating and maintenance costs can often quickly amortize the higher acquisition costs. Our experts will be happy to advise you on the best solution for your laboratory.
In order to achieve a low residual oxygen content, a very low ultimate vacuum is required. In some cases, four-stage chemistry diaphragm pumps with an ultimate vacuum of 0.6 mbar can be used to inert the airlock.
If the ultimate vacuum of the diaphragm pumps is not sufficient, this can be compensated for by additional pump-down cycles during airlock operation. If this procedure is not practical, we recommend two-stage rotary vane pumps with an ultimate vacuum in the range of 10-3 mbar.
A high pumping speed is required to evacuate the airlock as quickly as possible. Our experts will be happy to advise you on the optimum dimensioning of the vacuum pump.
In principle, it is possible to change the pump type at any time. However, you should clarify in advance whether the diaphragm pump meets the vacuum requirements for your glovebox. Our experts will be happy to advise you on this.
request for freeFor optimum performance, rotary vane pumps should warm up for approx. 30 minutes before starting the process. This is not necessary for diaphragm pumps. After operation, both pump types should run for 15 - 30 minutes with the gas ballast open in order to discharge any condensate that has formed.
All useful tips for operating your vacuum pump can be found here:
The vacuum pumps we recommend all have a small flange connection. If the connection of your system differs from the pump connection, you can find the right accessories from us.