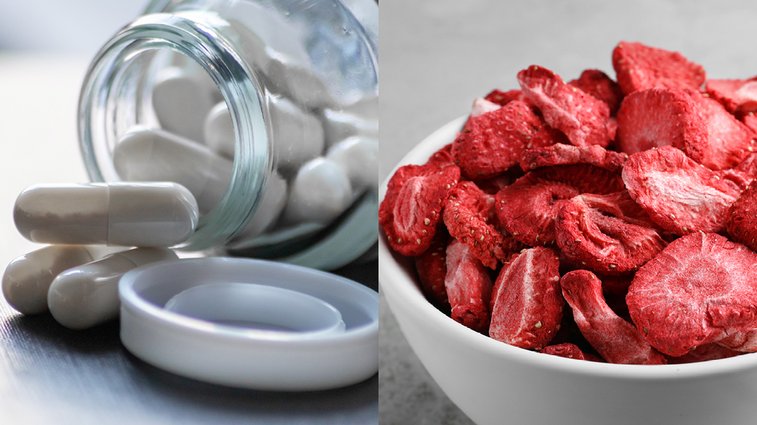
Thanks to freeze drying, medicines, for example, retain their effectiveness, and dried fruits retain their aromas.
© sunakri –stock.adobe.com, New Africa – stock.adobe.com
Why do instant coffee or dried fruit taste fresh? How can medicines and vaccines still be effective after months in storage? They are preserved using a very gentle process – freeze drying. The thermodynamic principle behind this is sublimation and it relies on vacuum technology.
To dry solids, the moisture contained in them – usually water – is often converted from the liquid state to the vapour (or gas) state by the application of heat, thereby removing it from the product. This can be done at atmospheric pressure or under vacuum. However, this process is unsuitable for many heat-sensitive products such as foodstuffs or medicines, as molecular structures can change, altering the flavor of food, or reducing the pharmaceutical efficacy.
The gentle freeze drying process is different: here the product is first deep-frozen in a step called pre-freezing. This converts any moisture it contains to a solid state, e.g. water then turns into ice. Then comes the step of primary drying. Reducing the pressure to the level below the triple point – the point at which a substance can exist as a solid, liquid, or gas – enables the transition of the ice crystals directly from the solid to the gaseous state; the solid ice never becomes a liquid. This phase transition is called sublimation. The rapid reduction of the pressure is necessary to avoid the occurrence of a liquid phase due to intermediate melting. During sublimation the physical state of the water changes, but the chemical properties of the product remain unchanged. In this way, all structures and characteristics of the end product are retained – such as colour, taste and efficacy.
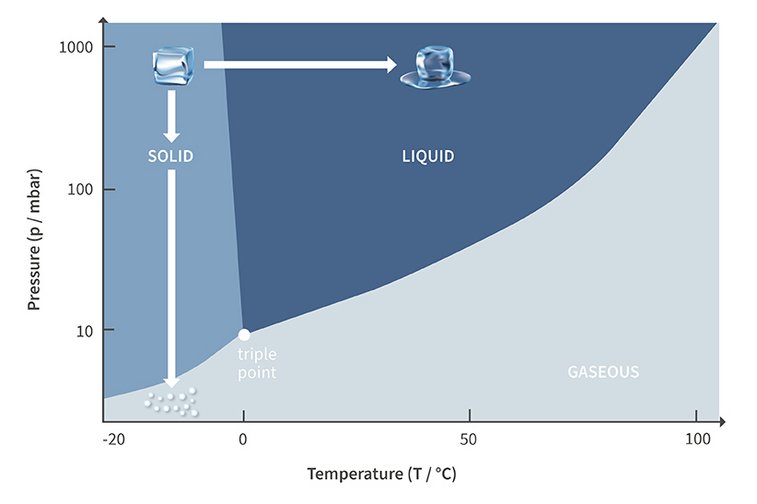
Phase diagram with transitions of the states of aggregation using water as an example; representation of sublimation and melting processes
This drying process based on sublimation is called lyophilization, or freeze drying. Two parameters are critical in this process: pressure and temperature. The triple point of water, for example, is 0°C and about 6 mbar. Below this triple point sublimation is possible. Reaching and maintaining the appropriate pressure level can only be achieved with appropriate vacuum technology.
Freeze drying process
The basic components of the freeze drying process are drying chamber, condenser with temperatures usually around -55°C or -85°C and vacuum pump.
In the first step, the product to be dried is deep-frozen, e.g. for laboratory samples typically in a freezer at temperatures below -20°C. Then the pre-frozen sample is placed on or in the drying chamber. The vacuum pump now evacuates the system to achieve the necessary process pressure for sublimation. In the example of -20°C cold water, this pressure is 1 mbar; however, for a reliable process, a pressure of approx. 10-1 mbar is recommended to prevent thawing. In general, the individual sublimation curve of each medium determines the course of the process; the lower the temperature, the lower the necessary process pressure.
During the following first sublimation step, the primary or main drying, most of the moisture is removed from the product. The resulting water vapour migrates towards the condenser, where it is converted back to the solid state of aggregation by the low temperatures prevailing there, i.e. re-sublimated to ice. The condenser thus assumes the function of a steam pump. For efficient process control it is essential that sublimation and re-sublimation form a state of equilibrium.
In most cases, the completed primary drying is followed by a second process step, the secondary or residual drying. Then the remaining, usually more strongly bound moisture is removed to the desired degree of drying. Even lower pressures are required for this, usually in the range of 10⁻2 to 10⁻3.
Vacuum pumps for freeze drying
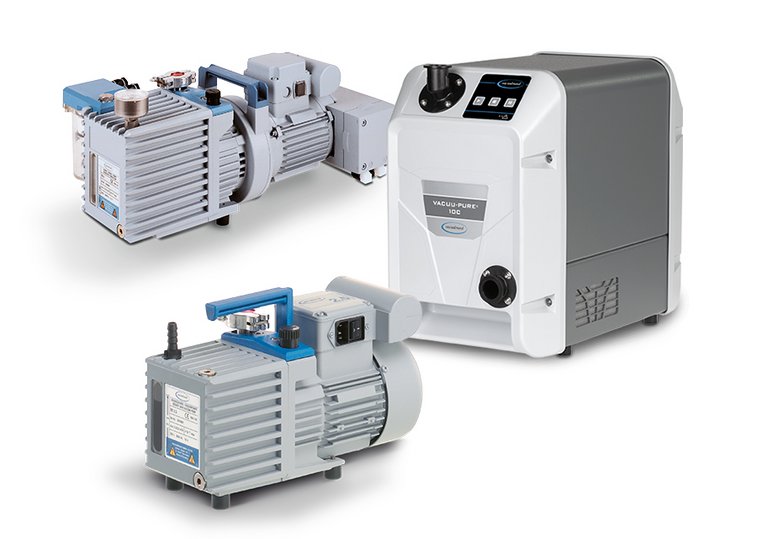
Different vacuum pumps can be used for freeze drying.
Depending on the requirements, different pump technologies are used for freeze drying systems in the laboratory. Often these are oil-sealed rotary vane pumps, but they are not chemically resistant. Chemistry-HYBRID pumps offer increased corrosion protection when working with condensing media.
For absolutely oil-free vacuum the VACUU·PURE dry screw pump can be used. For oil-free work with aggressive solvents the chemically resistant VACUU·PURE 10C version is the optimal solution.
Decisive for the choice of a vacuum pump:
- Vacuum performance with ultimate vacuum in the range of 10⁻3 for efficient process control in the freeze drying process (with primary and secondary drying)
- Sufficient pumping speed for rapid evacuation to achieve the sublimation conditions and to avoid defrosting of the product or sample
- High vapor and condensate tolerance for long-term reliability
- High chemical resistance when using aggressive solvents
- Oil-free technology for clean processes and products