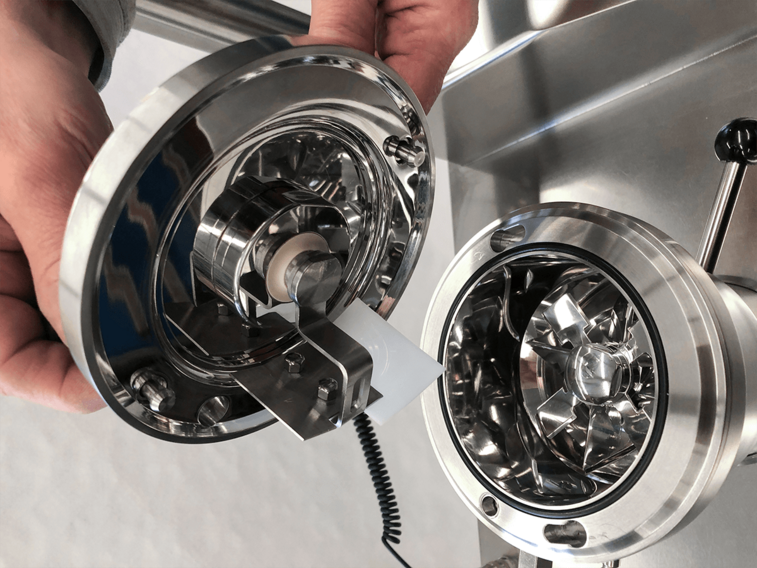
Modular and flexible laboratory mixer
© Somakon Verfahrenstechnik
The birthplace of many products – such as accumulators, pills or creams – is the laboratory mixer. In this interview, Wolfang Naton, founder of Somakon Verfahrenstechnik, provides insights into the diverse possibilities of modular and flexible systems for processes such as mixing, loading, granulating, drying and emulsifying. Vacuum pumps often play an indispensable role as silent helpers – both before and during critical process phases. They support the prevention of explosions, bubble formation and excessive moisture.
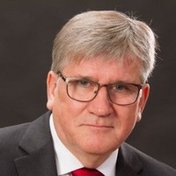
Wolfgang Naton, Managing Director of Somakon Verfahrenstechnik
© Wolfgang Naton
What inspired you to develop your own laboratory mixers?
Wolfgang Naton: The creation of new products always begins on a small scale – often in a laboratory mixer or generally in a compact system. During my career in galenics, I frequently encountered the limitations of conventional laboratory mixers. This led to the idea of founding Somakon Verfahrenstechnik in the year 2000, with the goal of developing modular and flexible laboratory-scale mixers. As a small company, we also leverage the opportunity to create tailor-made solutions for our customers. This combination of flexible technology and customized adaptations makes us problem-solvers in process engineering and allows us to occupy a unique niche in the industry.
What do you mean by modular and flexible?
Wolfgang Naton: Our mixers are truly multifunctional devices and can therefore be used in a variety of ways. The modular design allows you to change the container in just a few seconds. We offer vessel sizes from 0.5 to 14 liters, while our floor-standing mixer can even accommodate containers of up to 25 liters. Another advantage is the flexible selection of accessory tools: depending on the desired outcome, you can choose between powder tools and dispersing tools, for example. This enables our systems to produce both solid materials, such as through granulation, and semi-solid products, as in emulsification.
You can do a lot with our mixers: from loading porous particles with active ingredient solutions to wet granulation, pelletizing, coating and carrying out gentle drying processes. Of course, our mixers offer useful features such as temperature control, evacuation, and aeration. This makes them an essential part of complex processes – even for applications requiring working temperatures of over 160°C.
Vacuum pumps from VACUUBRAND are indispensable in process engineering, as they play a decisive role before and during many processes. Their use ranges from inert, i.e. oxygen-free processes, such as in battery development, to the gentle drying of various powders and granulates, and even the bubble-free emulsification of semi-solid products, such as pharmaceutical creams and gels. (Wolfgang Naton)
How important is vacuum in process engineering?
Wolfgang Naton: In most cases, a vacuum of down to 10 mbar is sufficient to achieve the desired results. Diaphragm vacuum pumps, which optimally cover this pressure range, are particularly suitable for this purpose.
- Before the start of some processes, vacuum is crucial for the inerting of the container. In this common and important procedure, the goal is to protect oxygen-sensitive products such as enzymes or prevent the formation of explosive mixtures, such as during the development of battery materials. To achieve this, we must remove the oxygen from the system, and this can only be done through effective evacuation. Precise control of the vacuum pressure is therefore essential. Afterwards, the container is specifically filled with inert gases such as nitrogen or argon when a process under normal pressure is more advantageous.
- Vacuum is used again during several process steps, such as for gentle drying. This is the case, for example, in the chemical modification of finely dispersed powders for the development of catalysts. In this surface treatment, we load carrier materials e.g. by spraying them with active ingredients dissolved in liquids. If the material becomes too wet, we use vacuum and temperature to gently evaporate the excess liquid. The process steps of spraying and evacuating are repeated until the desired active ingredient concentration is achieved. This sequential process requires a reliable pump that controls the vacuum according to the vapor pressure or boiling point of the substances used. Vacuum is also essential during emulsification, such as in the production of pharmaceutical creams or gels. Otherwise, bubbles would form in the product.
Which specific vacuum pumps do you use?
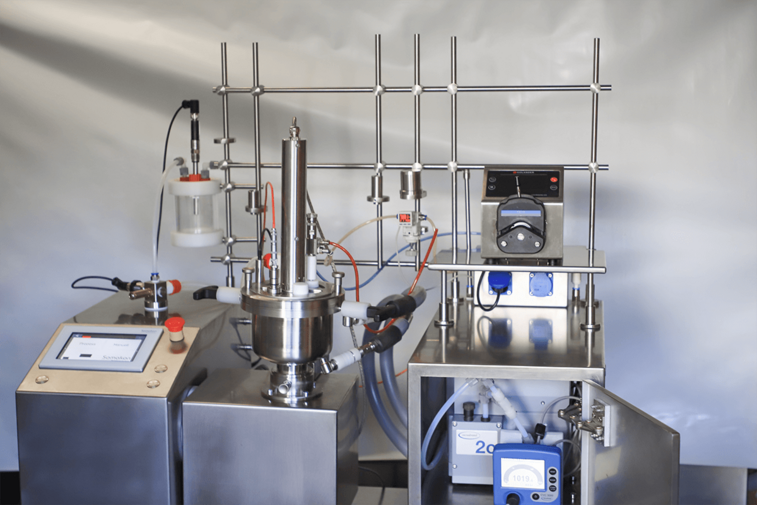
Laboratory system from Somakon in combination with vacuum pump from VACUUBRAND
© Somakon Verfahrenstechnik
Wolfgang Naton: I have been working with VACUUBRAND vacuum pumps since the 1980s, first in the chemical industry and now in process engineering. Their reliability is what sets them apart for me. Chemical resistance is particularly important to ensure the pumps are unaffected by aggressive solvent vapors. Additionally, they are ideal for continuous operation over several hours.
As a built-in version for systems, I use the MZ 2C NT diaphragm vacuum pump because it is particularly space-saving when installed in a cabinet. Additionally, I always carry the PC 3001 VARIOpro diaphragm vacuum pump for customer visits, as it already includes an integrated separator and a controller for precise vacuum regulation. This makes it ideal for flexible laboratory use, providing on-site support for experiments requiring vacuum. Ultimately, both pumps from VACUUBRAND offer the quality and flexibility that both my customers and I need for daily work. I am happy to remain loyal to these trusted devices.
We would like to thank Wolfgang Naton for the interview.