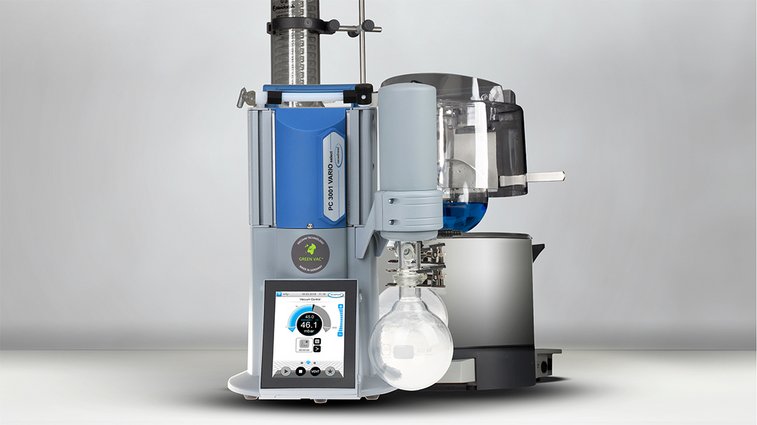
Vacuum pumping unit PC 3001 VARIO select on the rotary evaporator
Vacuum enables the evaporation of material mixtures at low temperatures and short process times. This principle is used in rotary evaporation, a fast and gentle separation process for heat-sensitive substances, among others, with different boiling points.
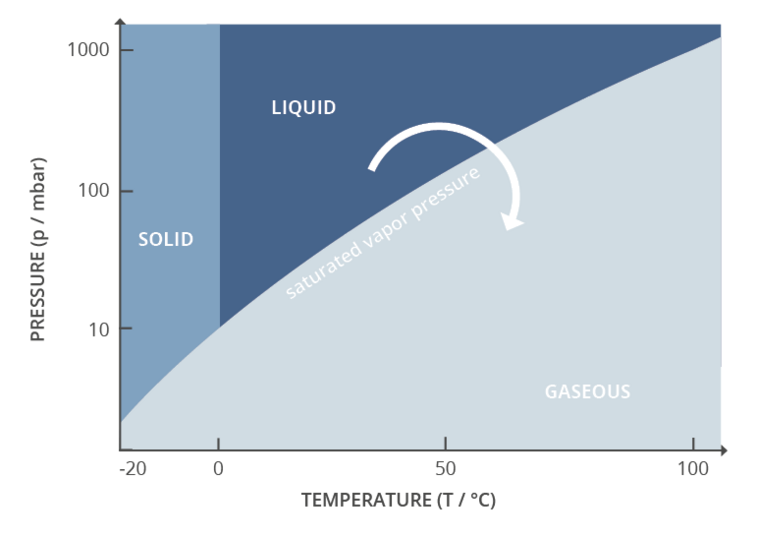
Phase diagram with transitions of the states of aggregation, representation of evaporation
A frequently used separation process for mixtures of substances is evaporation. In this process, substances with different boiling points are separated from each other: the more volatile substance, or impurities, evaporate with the addition of heat. This leaves behind the less volatile product, typically as a solid or a concentrate, in isolation.
A special type of evaporation is rotary evaporation – it allows higher evaporation rates at lower temperatures and thus a gentle separation which is well-suited for work with heat-sensitive compounds such as active pharmaceutical ingredients (APIs). By applying vacuum, boiling temperatures are lowered and heat-sensitive materials are protected, even as high-boiling point solvents evaporate at modest temperatures.
Vacuum is therefore an important process parameter in rotary evaporation. Together with temperature, it controls the evaporation process. Every evaporation process is fundamentally driven by the vapor pressure or boiling pressure curve for that substance. The vapor pressure curve simply gives the pressure at which a substance will transition from the liquid phase to the gas phase for a given temperature. The lower the process pressure, the lower the required temperature. Vacuum is an active control parameter for process control, since very rapid adjustments can be made. Active control of temperature is considerably slower and therefore not suitable as an adaptive process parameter in this special application. Vacuum control is used to adjust the pressure to maximize process efficiency, minimize process time, and maintain safe working conditions.
How does vacuum control work?
In rotary evaporation, the vacuum pump combined with an electronic vacuum control adjusts the vacuum level to an optimal level.
One way to control the vacuum level is with a valve on the vacuum line, using what’s often referred to as ‘two-point control.’ The user defines a setpoint on an electronic vacuum controller. The controller reads the actual process pressure from a vacuum sensor and opens or closes the valve accordingly. The result is that the controller and pump will work together to hold the vacuum level as close as possible to the user-provided setpoint. Some oscillation around the setpoint is typical with two-point control. It is even possible to automatically detect the specific vapour pressures of low, medium and high boiling solvents. This is particularly useful because the real vapor pressure of a solvent within a mixture of substances deviates from its boiling point in pure form – as shown in a solvent table or on a vapor pressure curve.
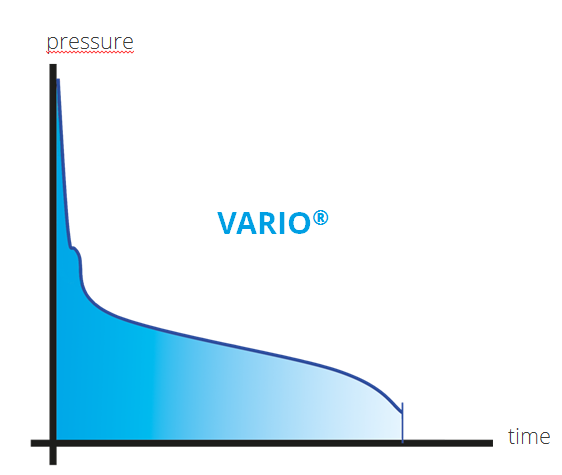
The VARIO® vacuum control allows continuous vapor pressure tracking
For processes where maximum precision is needed, speed-controlled adaptive VARIO® technology delivers precise vacuum control without the pressure fluctuations that occur with two-point control. Even as the vapor pressure of the solution changes with the change in relative concentration of the solvents in the solution during the evaporation process, the electronic vacuum controller automatically adjusts the pump’s motor speed continuously and with greater precision than can be achieved with two-point control, thus continuously tracks the optimum process condition. This means that the evaporation rate is optimised at all times, achieving even shorter process times and preventing losses from over-boiling and foaming.
Process of rotary evaporation
How does a vacuum pump work with a rotary evaporator? The rotary evaporator consists of a heated water bath, a rotating evaporation flask that contains the mixture to be separated, and a chilled condenser with a condensate collection flask. The vacuum pump is a separate unit connected to the rotary evaporator on the condenser side via vacuum tubing.
The evaporation flask with the mixture of substances is first immersed in the heated water bath. The rotation and shape of the flask result in better heat distribution and greater surface area than in a distillation column, accelerating the evaporation process. By adding heat and reducing the pressure inside the rotary evaporator through the vacuum pump, the substance with lower boiling point evaporates. The vapour travels to the cooled condenser and condenses there. It thus changes from the gaseous state to the liquid state again and is collected in the receiving flask below the condenser. The desired product remains isolated in the evaporation flask, typically in the form of a solid or a concentrated solution.
When setting up an evaporation process in a rotary evaporator, the “Delta 20” rule of thumb can help to optimize the evaporation. The Delta 20 rule refers to the temperature gradients between the heating bath, solvent vapor, and the condenser. The effective vapour temperature is approx. 20°C lower than the set temperature at the heating bath, as the evaporation process gives off energy, and thus heat, from the liquid mixture. For efficient condensation, the cooling temperature at the condenser should be at least 20°C lower than the effective vapour temperature.
Vacuum pumps for rotary evaporation

Vacuum pumps and pumping units for different boiling points and volumes
The choice of the appropriate vacuum pump depends on the specific boiling points of the substances used and the volume of the rotary evaporator. In general, chemistry diaphragm pumps that are highly resistant to both organic solvents and aggressive chemicals are recommended. In addition, multi-stage vacuum pumps are used in rotary evaporation processes to ensure sufficient vacuum depth and pumping speed. VACUUBRAND offers a complete product range which includes basic pumps, advanced pumps with additional capabilities such as solvent recovery, and fully automatic pumps with adaptive VARIO® technology. There are also vacuum pumps that can supply vacuum to two evaporators simultaneously, each with independent vacuum control.
Boiling points and required vacuum:
- Low boiling solvents: two-stage chemistry diaphragm pumps (vacuum down to 7 mbar)
- Medium and high boiling solvents: three- and four-stage chemistry diaphragm pumps (vacuum to 1.5 mbar or < 1 mbar)
Volume and required pumping speed:
- Benchtop rotary evaporators with volumes up to 5 litres: chemistry diaphragm pumps with pumping speeds of approx. 1-2 m3/h
- Large-scale rotary evaporators with volumes up to 20 litres: chemistry diaphragm pumps with pumping speeds of approx. 3-5 m3/h